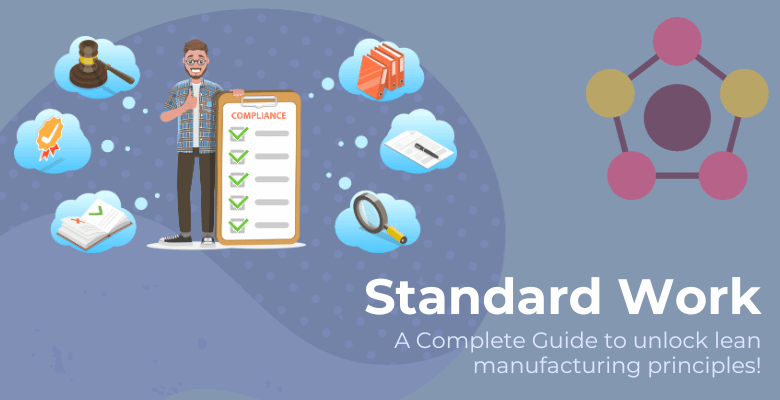
Standard Work Essentials: Optimizing Your Business Operations and Lean Manufacturing
Standard Work is not a static concept; it’s a living, evolving system that adapts to the needs of your organization. Overcome resistance to change, leverage technology, and benchmark against industry standards. Whether you’re a manufacturing powerhouse, a service-oriented business, or an innovative tech firm, the principles of Standard Work can elevate your operations to new heights.
Table Of Content
I. Introduction
II. Key Components of Standard Work
III. Benefits of Implementing Standard Work
IV. Real-Life Examples
V. How to Establish Standard Work in Your Business
VI. Overcoming Challenges
VII. Standard Work in a Digital Environment
VIII. Case Study: Someka.net’s Experience with Standard Work
IX. Comparison with Industry Standards
X. Future Trends in Standard Work
XI. Standard Work and Six Sigma
XII. Conclusion
XIII. FAQ’s
I. Introduction
In the dynamic landscape of business operations, having a well-defined and structured approach is paramount. This is where “Standard Work” comes into play, serving as the backbone of organizational efficiency.
Brief Definition of Standard Work
At its core, Standard Work refers to the documented and established set of processes, procedures, and guidelines that outline how tasks are to be executed within a business. It acts as a comprehensive playbook, ensuring that each operation is conducted consistently and systematically.
Importance in Business Operations
The significance of Standard Work in business operations cannot be overstated. It provides a stable framework that fosters clarity and uniformity in tasks, minimizing variations and potential errors. This consistency translates into enhanced productivity, as employees can follow a structured approach, reducing the likelihood of misunderstandings or deviations from the established norms.
Moreover, Standard Work is instrumental in quality improvement. By setting a standard for each task, businesses can identify and rectify inefficiencies, leading to a continuous enhancement of processes. This, in turn, contributes to the overall effectiveness and competitiveness of the organization.
In the fast-paced world of commerce, adaptability is key. Standard Work acts as a reliable anchor, ensuring that even in the face of change, the fundamental operations remain steadfast. This adaptability is crucial in a business environment where agility and responsiveness are prerequisites for success.
Lean Manufacturing
Standard Work is one of the key components of lean manufacturing.
Lean manufacturing, often heralded as a paradigm shift in production philosophy, is a systematic approach aimed at eliminating waste, optimizing efficiency, and creating value for customers. Originating from the Toyota Production System, this methodology transcends the confines of a mere manufacturing strategy; it’s a holistic philosophy that permeates every facet of organizational operations.
At its core, lean manufacturing focuses on the relentless pursuit of efficiency by identifying and eliminating any activity that doesn’t contribute value to the end product or service. This waste-reduction ethos encompasses various forms of waste, including overproduction, excess inventory, unnecessary motion, defects, and underutilized employee skills. By minimizing waste, lean manufacturing not only enhances productivity but also aligns with sustainability goals by reducing environmental impact.
Central to the lean philosophy is the concept of continuous improvement, encapsulated in the Japanese term “Kaizen.” This principle encourages a culture of ongoing enhancement, empowering every employee to contribute ideas for incremental improvements. This collaborative approach fosters a sense of ownership and engagement, creating a workplace that thrives on innovation and adaptability.
Lean manufacturing extends beyond the shop floor, permeating supply chain management, product development, and even administrative processes. By adopting practices like Just-In-Time (JIT) inventory management and pull systems, organizations can respond more dynamically to customer demand, minimizing lead times and reducing excess inventory costs.
In conclusion, lean manufacturing is more than a set of tools and techniques; it’s a transformative philosophy that challenges traditional notions of production. By championing efficiency, waste reduction, and continuous improvement, lean manufacturing lays the groundwork for organizations to not only survive but thrive in the ever-evolving landscape of modern business.
II. Key Components of Standard Work
In delving into the intricacies of Standard Work, it’s imperative to understand the core components that make this systematic approach effective and indispensable.
Clear Procedures and Instructions
At the heart of Standard Work lie crystal-clear procedures and instructions. This component ensures that every task is delineated in detail, leaving no room for ambiguity. Clarity in instructions not only facilitates smoother execution but also acts as a reference point for employees, reducing the likelihood of errors. From step-by-step guides to detailed process maps, having explicit procedures is the cornerstone of effective Standard Work.
A procedural framework is a structured set of guidelines and steps that govern how tasks and processes should be carried out within an organization, ensuring consistency and reliability.
Defined Roles and Responsibilities
Another crucial element is the explicit definition of roles and responsibilities within the standardized processes. By clearly outlining who is responsible for each aspect of a task, Standard Work establishes accountability. This not only prevents confusion but also fosters a sense of ownership among employees. When everyone understands their role in the broader context, collaboration becomes more seamless, promoting a culture of efficiency and teamwork.
– This image is from the RACI Matrix of Responsibility Assigment Tool by Someka –
Consistency and Repetition
Consistency and repetition form the backbone of Standard Work. By adhering to established procedures consistently, organizations create a reliable and predictable work environment. This consistency minimizes variations in output, ensuring that the end result meets the desired standard each time. Repetition ingrains these processes into the organizational culture, fostering a level of expertise and efficiency that can only be achieved through continuous practice.
– This is the Chart View from Standard Work Template by Someka –
Operational norms are established standards and behaviors that define the acceptable and expected conduct within an organization, fostering a consistent and harmonious work environment.
In essence, the key components of Standard Work synergize to create a structured, accountable, and consistent framework, laying the groundwork for operational excellence within any business.
III. Benefits of Implementing Standard Work
Embarking on the journey of implementing Standard Work brings forth a myriad of advantages that resonate across the entire spectrum of business operations, from the shop floor to the boardroom.
Increased Efficiency
One of the primary merits of embracing Standard Work is the marked increase in operational efficiency. When tasks are carried out according to standardized procedures, the workflow becomes more streamlined and predictable. This efficiency surge translates to saved time, reduced costs, and an overall boost in productivity. Employees can focus on executing tasks rather than deciphering processes, leading to a workplace that hums with optimized performance.
Quality Improvement
Standard Work serves as a steadfast guardian of quality within an organization. By establishing standardized procedures, businesses can meticulously identify and rectify inefficiencies, reducing the margin for errors. Consistency in processes directly correlates with consistency in output, ensuring that products or services meet or exceed predefined quality standards. This commitment to quality not only enhances customer satisfaction but also fortifies the reputation of the organization in the market.
Streamlined Processes
In the realm of business, complexity often begets inefficiency. Standard Work acts as a simplifying force, streamlining processes to their most essential components. This simplicity not only makes tasks more manageable for employees but also facilitates quicker decision-making processes. Streamlined operations lead to agility, a crucial trait in an ever-evolving business landscape. The ability to navigate processes with ease enhances adaptability, enabling businesses to respond promptly to changing market demands.
In essence, the benefits of implementing Standard Work extend beyond mere efficiency gains; they encompass a holistic transformation of the operational landscape, fostering a culture of quality, consistency, and adaptability.
IV. Real-Life Examples
Examining real-life applications of Standard Work reveals its transformative power across diverse industries, underscoring its role as a catalyst for success.
Success Stories from Various Industries
In manufacturing, adherence to Standard Work has yielded remarkable success stories. Automotive giants have implemented standardized processes on the assembly line, resulting in reduced defects, increased production speed, and substantial cost savings. The aviation industry, too, has harnessed Standard Work to enhance safety protocols, leading to fewer errors in maintenance procedures and, consequently, a safer air travel experience.
Moving beyond manufacturing, the healthcare sector has embraced Standard Work to improve patient care. From standardized nursing procedures to streamlined administrative processes, healthcare organizations have witnessed enhanced efficiency, reduced errors, and ultimately, improved patient outcomes.
In the technology sector, especially within Europe, companies leveraging Standard Work in software development have seen accelerated project timelines and reduced debugging efforts. The region’s emphasis on standardized coding practices and development procedures reflects a broader trend across software development Europe, contributing to a more efficient and error-free software development lifecycle.
Impact on Productivity and Bottom Line
The impact of Standard Work on productivity and the bottom line is unmistakable. Companies that have integrated standardized processes experience heightened productivity due to streamlined workflows and reduced time spent on deciphering ambiguous procedures. This newfound efficiency directly translates into substantial cost savings, contributing to an improved bottom line.
Moreover, the predictability and consistency fostered by Standard Work enable organizations to allocate resources more effectively. Whether it’s optimizing workforce deployment or managing inventory, the standardized approach provides a strategic advantage, enhancing overall operational efficiency.
These real-life examples underscore the versatility of Standard Work, showcasing its ability to drive success across industries, improve productivity, and fortify the financial health of organizations.
V. How to Establish Standard Work in Your Business
Implementing Standard Work is a strategic endeavor that demands a meticulous approach. Here’s a step-by-step guide on how to establish Standard Work effectively within your business.
Assessing Current Processes
The initial step involves a comprehensive assessment of your current processes. Identify existing workflows, pinpoint areas of variability, and assess the efficiency of each task. This critical evaluation serves as the foundation for crafting standardized procedures. By understanding the intricacies of your current operations, you pave the way for targeted improvements and set the stage for a seamless transition to Standard Work.
Creating Detailed Procedures
With a clear understanding of existing processes, the next step is to craft detailed and unambiguous procedures. Each task should be systematically documented, outlining step-by-step instructions, timelines, and key performance indicators. Embrace clarity in language and structure to ensure that employees can easily comprehend and follow the standardized procedures. Utilize visual aids such as flowcharts or diagrams to enhance understanding, creating a comprehensive guide that leaves no room for interpretation.
Employee Training and Involvement
Introducing Standard Work necessitates a collaborative effort involving all stakeholders, with a focus on comprehensive employee training and active involvement. Provide thorough training sessions to familiarize employees with the standardized procedures. Foster an environment where questions and feedback are encouraged, ensuring that everyone is on the same page. Actively involve employees in the creation and refinement of Standard Work to capitalize on their insights and expertise. This collaborative approach not only facilitates a smoother implementation but also instills a sense of ownership among the workforce.
By systematically assessing, documenting, and involving employees, the establishment of Standard Work becomes a purposeful and collaborative initiative, laying the groundwork for sustained operational excellence within your business.
VI. Overcoming Challenges
Navigating the implementation of Standard Work is not without its challenges. Recognizing and effectively addressing these hurdles is crucial to ensuring a successful integration.
Resistance to Change
Resistance to change is a common obstacle when introducing new processes, and Standard Work is no exception. Employees, accustomed to established routines, may initially resist the shift towards standardized procedures. To overcome this challenge, it is imperative to communicate the benefits of Standard Work transparently. Emphasize how it streamlines processes, reduces errors, and ultimately contributes to a more efficient and rewarding work environment. Encourage open dialogue, address concerns, and involve employees in the decision-making process to foster a sense of ownership in the transition.
Continuous Improvement Strategies
The essence of Standard Work lies in its adaptability and continuous improvement. Organizations must establish strategies to not only overcome initial resistance but also to perpetually enhance and refine their standardized processes. Implement feedback loops that allow employees to share insights and suggest improvements.
Regularly review and update procedures to incorporate evolving best practices and technological advancements. By embedding a culture of continuous improvement, businesses can ensure that Standard Work remains a dynamic and evolving force, capable of meeting the ever-changing demands of the business landscape.
Work consistency refers to the uniformity and reliability of tasks and processes within an organization. It ensures that work is executed in a standardized manner, reducing variations.
In essence, overcoming challenges in implementing Standard Work involves addressing the human element through effective communication and involving employees in the process. Simultaneously, it requires a commitment to continuous improvement, ensuring that Standard Work remains a living, breathing system that adapts and evolves alongside the organization it serves.
VII. Standard Work in a Digital Environment
The integration of Standard Work into a digital environment marks a significant evolution, leveraging technology to enhance efficiency and collaboration within an organization.
Utilizing Technology for Automation
In the digital era, automation is the linchpin of operational efficiency, and Standard Work seamlessly aligns with this technological trend. By leveraging automation tools, routine and time-consuming tasks can be executed with precision, freeing up valuable human resources for more complex and strategic endeavors. Whether it’s automating data entry, document generation, or communication workflows, technology transforms Standard Work into a dynamic and responsive system.
The synergy between Standard Work and automation not only accelerates processes but also minimizes the risk of human error. Tasks executed with the precision of automation contribute to a consistent and error-free workflow, elevating the overall quality of operations.
Integrating with Project Management Tools
The marriage of Standard Work with project management tools forms a powerful alliance, enhancing collaboration and transparency across projects. Integrating standardized procedures with project management platforms creates a centralized hub where teams can access and execute tasks seamlessly. This integration streamlines communication, facilitates real-time tracking of progress, and ensures that everyone is aligned with the standardized processes.
Furthermore, project management tools provide invaluable insights into the performance of standardized workflows. Metrics such as task completion times, resource utilization, and project milestones become readily available, enabling organizations to continually refine and optimize their Standard Work based on data-driven insights.
– This image is from Someka’s SIPOC Excel Template –
For example, if you’re using a project management tool like Jira, you can take advantage of their issue template that optimizes your workflow by offering pre-defined fields specific to your standardized tasks. This not only saves time and effort but also ensures consistency and quality across all projects.
In essence, the digitalization of Standard Work not only embraces the efficiencies afforded by automation but also capitalizes on the collaborative prowess of project management tools, positioning organizations at the forefront of technological innovation in their pursuit of operational excellence.
VIII. Case Study: Someka.net’s Experience with Standard Work
Delving into the real-world application of Standard Work, the experience of Someka.net serves as an illuminating case study, highlighting the tangible benefits and transformative impact on operations.
Implementing Standard Work in Operations
Someka.net, a leading provider of Excel and Google Sheets templates, recognized the need for a standardized approach to enhance their operational efficiency. Implementing Standard Work became a pivotal strategy to streamline their diverse range of tasks, from template creation to customer support.
By meticulously assessing their existing processes, Someka.net identified areas for improvement and developed detailed standardized procedures. This included clearly defined steps for template development, customer inquiry responses, and order fulfillment. The structured approach provided a roadmap for their team, ensuring consistency and precision in every facet of their operations.
Tools for Standard Work Implementation
Unlock the Full Potential of Standard Work with Someka.net’s Specialized Templates!
Embarking on the journey of implementing Standard Work is made even more seamless with Someka.net’s range of specialized templates. Our Manufacturing KPI Dashboard Excel Template provides a comprehensive view of key performance indicators, empowering you to make data-driven decisions.
For those delving into the realm of Six Sigma, our Six Sigma Calculator Excel Template offers a sophisticated tool for statistical analysis and process improvement.
Navigate the intricacies of risk management with our FMEA Excel Template, ensuring a robust approach to identifying and mitigating potential issues.
– This Dashboard is from Someka’s FMEA Google Sheets Template –
In the pursuit of operational excellence, our 5S Audit Scorecard Excel Template serves as a valuable asset, facilitating the systematic evaluation of workplace organization and efficiency.
– This is the Dashboard Section of Someka’s 5S Scorecard Audit Template –
Finally, for project management aligned with Standard Work principles, our WBS Gantt Chart Excel Template becomes your go-to tool, offering a visual representation of tasks and timelines.
At Someka.net, we understand the nuances of implementing Standard Work, and our templates are meticulously crafted to complement and enhance your efforts. Empower your organization with these tools, designed to streamline processes, boost efficiency, and elevate your operational standards. Take the next step towards excellence with Someka.net’s tailored templates—your partners in the pursuit of standardized success.
Measuring Success Metrics
The implementation of Standard Work at Someka.net yielded tangible results that reverberated throughout their operations. Key success metrics were carefully monitored to gauge the impact of standardized procedures.
- Operational Efficiency: Standard Work streamlined template creation, reducing development times and allowing Someka.net to offer a wider array of products.
- Customer Satisfaction: Clear procedures in customer support enhanced response times and resolution efficiency, leading to improved customer satisfaction rates.
- Order Fulfillment: Standardized processes in order fulfillment contributed to a reduction in errors and faster delivery times, bolstering customer trust.
These success metrics not only reflected in improved internal processes but also manifested in Someka.net’s bottom line. The structured approach of Standard Work enhanced productivity, reduced costs, and positioned Someka.net as a more agile and customer-focused organization.
– This image is from Manufacturing KPI Dashboard Google Sheets Template by Someka –
Performance standards are predefined criteria used to assess and measure the effectiveness and quality of work. They serve as benchmarks for evaluating individual and organizational performance.
In essence, the case study of Someka.net underscores the transformative power of Standard Work, showcasing its ability to revolutionize operations and drive tangible business outcomes.
IX. Comparison with Industry Standards
Comparing Standard Work practices with industry standards is a strategic exercise that allows organizations to gauge their performance, identify areas for improvement, and stay agile in an ever-evolving business landscape.
Benchmarking Practices
Benchmarking Standard Work practices involves evaluating your organization’s processes against industry benchmarks and best practices. By doing so, businesses can gain valuable insights into their competitiveness and efficiency. Benchmarking provides a yardstick for measuring performance metrics such as process cycle times, error rates, and resource utilization, enabling organizations to identify areas where they excel and pinpoint opportunities for enhancement.
How do best practices influence operational excellence? Best practices are recognized methods or techniques that have proven to be effective in achieving superior results. In a business context, adhering to best practices contributes to operational excellence.
Understanding how other industry leaders approach Standard Work allows for a holistic perspective, inspiring innovative ideas and practices. By adopting benchmarking as a regular practice, businesses can continuously refine their Standard Work, ensuring they remain at the forefront of industry standards.
Adapting to Evolving Standards
In a dynamic business environment, industry standards are in a perpetual state of evolution. Standard Work, to remain effective, must be adaptable and responsive to these changes. Organizations need to actively monitor industry trends, technological advancements, and regulatory shifts that might impact their operations.
Adapting to evolving standards involves a proactive approach to updating and refining Standard Work procedures. Regular reviews and assessments ensure that standardized processes align with the latest industry practices. Embracing a culture of continuous improvement allows organizations not only to stay compliant with industry standards but also to position themselves as innovators within their sector.
In essence, the comparison with industry standards is not merely a performance evaluation but a strategic tool that empowers organizations to stay agile, competitive, and responsive to the ever-changing landscape of their industry.
X. Future Trends in Standard Work
Looking ahead, the landscape of Standard Work is poised for transformative shifts, driven by technological advancements and the evolving nature of work environments.
Incorporating AI and Automation
The future of Standard Work is intricately woven with the threads of artificial intelligence (AI) and automation. As technology continues to advance, organizations are increasingly integrating AI and automation into their standardized processes. AI can analyze vast datasets, offering insights for refining and optimizing procedures. Automation, on the other hand, streamlines repetitive tasks, freeing up human resources for more complex and creative endeavors.
Incorporating AI and automation into Standard Work not only enhances efficiency but also contributes to a more agile and responsive organizational structure. Tasks that once required significant manual intervention can now be executed with unprecedented speed and precision, propelling Standard Work into a new era of productivity.
Adapting to Remote Work Environments
The rise of remote work has become a defining feature of the modern workplace, and the future of Standard Work embraces and adapts to this paradigm shift. With teams distributed across various locations, the need for standardized processes becomes even more pronounced. Standard Work provides a common framework that ensures consistency and collaboration, irrespective of physical distances.
Adapting Standard Work to remote environments involves leveraging digital tools and platforms for seamless communication and task execution. Cloud-based collaboration tools, project management software, and virtual communication channels become integral components of the standardized toolkit. As organizations redefine the concept of the workplace, Standard Work becomes a unifying force that bridges the gap between traditional and remote work environments.
In essence, the future trends in Standard Work herald an era of unprecedented efficiency through the incorporation of AI and automation, coupled with a seamless adaptation to the dynamics of remote work environments. This evolution positions Standard Work as a cornerstone of organizational success in the years to come.
XI. Standard Work and Six Sigma
The synergy between Standard Work and Six Sigma represents a powerful alliance, combining structured processes with data-driven methodologies to achieve unparalleled levels of efficiency and quality.
What’s Six Sigma?
Six Sigma is a methodology rooted in statistical analysis and data-driven decision-making. It aims to eliminate defects and variations in processes, ultimately enhancing quality and reducing inefficiencies. The term “Six Sigma” refers to a statistical measure that signifies a process is producing fewer than 3.4 defects per million opportunities—a level of precision and consistency that aligns seamlessly with the principles of Standard Work.
Relation between Six Sigma and Standard Work
At its core, Six Sigma and Standard Work share a common goal: the pursuit of operational excellence. Standard Work provides the structured framework, the documented procedures, and the consistency required for successful Six Sigma implementation. Six Sigma, in turn, brings a rigorous methodology for measuring, analyzing, improving, and controlling processes.
– This chart is from Six Sigma Calculator by Someka –
The relationship between Six Sigma and Standard Work is symbiotic. While Standard Work sets the stage by establishing clear and standardized procedures, Six Sigma acts as a continuous improvement mechanism. It identifies variations within these standardized processes, analyzes the root causes, and implements data-driven solutions to enhance efficiency and quality.
In essence, the integration of Six Sigma and Standard Work creates a harmonious loop of continuous improvement, where the structured foundation of Standard Work aligns seamlessly with the analytical prowess of Six Sigma, leading to optimized processes and heightened organizational performance.
XII. Conclusion
As we conclude our exploration of Standard Work, it becomes evident that this systematic approach is not merely a set of procedures but a catalyst for organizational excellence. Let’s revisit the key points that underscore its significance and offer a final push towards implementation.
Recap of Key Points
Throughout this journey, we’ve delved into the core components of Standard Work, its real-life applications, and the transformative impact it can have on operations. We’ve witnessed its adaptability in a digital environment, explored challenges, and envisioned its future in the dynamic landscape of work. The case study of Someka.net and the integration with Six Sigma showcased practical success stories, emphasizing the tangible benefits of this approach.
From increased efficiency and quality improvement to adaptability and collaboration, Standard Work emerges as a linchpin for organizations striving for operational excellence. Its role in a digital world, adaptation to evolving standards, and the future trends involving AI and automation solidify its relevance in the ever-changing business panorama.
Encouragement for Implementation
Now, as you stand at the crossroads of knowledge and action, the call to implement Standard Work reverberates. Embrace this structured approach as more than a methodology; it’s a commitment to efficiency, consistency, and continuous improvement. Begin by assessing your current processes, crafting detailed procedures, and involving your team in the journey.
In conclusion, Standard Work is not just a path to success; it’s the blueprint for sustained excellence. Embrace it, refine it, and let it become the heartbeat of your organization’s journey towards operational mastery. The road may be challenging, but the rewards in efficiency, quality, and adaptability are immeasurable. The future of your organization, guided by the principles of Standard Work, awaits your proactive embrace.
XIII. FAQ’s
Questions on Concepts
- What are standard operating procedures?
Standard Operating Procedures (SOPs) are documented instructions detailing the steps, activities, and responsibilities required to complete tasks in a standardized manner within an organization.
- What do workflow guidelines entail?
Workflow guidelines are systematic instructions that outline the sequential steps and interactions necessary to complete a specific process efficiently. They provide a structured pathway for task execution.
- What is an efficiency protocol in a business context?
An efficiency protocol in a business context refers to a set of guidelines and rules designed to optimize processes and resource utilization, ultimately enhancing overall operational efficiency.
- What is the role of work standards in a structured organization?
Work standards outline the expected level of performance and quality for tasks and processes. They provide a benchmark for evaluating and maintaining consistency in work output.
- What is a methodology blueprint?
A methodology blueprint is a comprehensive plan or guide that outlines the systematic approach and methods to be employed in a particular business methodology, ensuring a consistent and replicable process.
Implementation Questions
- What role do operational rules play in maintaining a standardized environment?
Operational rules are established regulations and directives that govern behavior, processes, and tasks within an organization, ensuring adherence to standards and protocols.
- How are task protocols established and implemented in business operations?
Task protocols are predefined sets of rules and guidelines that dictate how specific tasks should be performed. They contribute to consistency and efficiency in task execution.
- How are job specifications defined and adhered to within an organization?
Job specifications outline the qualifications, skills, responsibilities, and requirements for a particular job role within an organization, providing clear expectations for both employers and employees.
- How do task guidelines contribute to task execution within an organization?
Task guidelines are detailed instructions specifying how particular tasks should be executed. They provide clarity and uniformity in task performance across the organization.
- What constitutes an operational framework?
An operational framework is a structured model that defines the key components, processes, and interactions within an organization. It serves as a guide for achieving operational objectives.
- How is task consistency maintained in business processes?
Task consistency is maintained by adhering to established guidelines and protocols, ensuring that tasks are executed in a uniform and reliable manner across the organization.
- How do process standards contribute to organizational efficiency?
Process standards are predefined criteria and benchmarks established to ensure consistency, quality, and efficiency in organizational processes. They serve as a reference for optimal performance.
Recommended Readings:
Six Sigma Methodology: Complete Overview